In businessand engineering, new product development (NPD) covers the complete process of bringing a new product to market, renewing an existing product or introducing a product in a new market. A central aspect of NPD is product design, along with various business considerations. New product development is described broadly as the transformation of a market opportunity into a product available for sale. The products developed by an organisation provide the means for it to generate income.
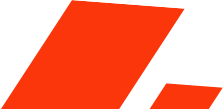
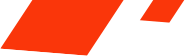
Insight of SCMC
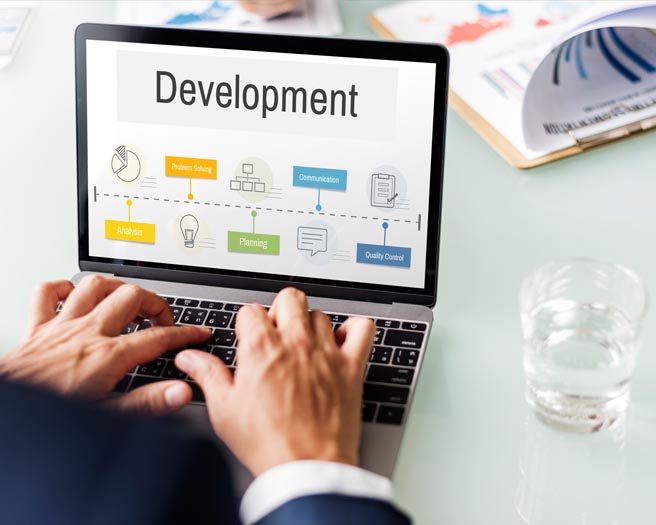
1. New product development
2. New materials development
New material development transforms design and manufacturing processes. The use and availability of new materials sometimes not merely enhance an existing design or process, it revolutionises it entirely. The new materials development industry is at the forefront of the world’s scientific and technological advancements. Improvements in materials range from increasing strength to increase flexibility to decreasing production costs. Oftentimes, high temperature furnaces are utilized to test and create these improvements. The types of new materials being developed include chemicals, polymers, ceramics, metals, nanomaterials, and more. As advancements occur in new materials, pathways are made for innovations in a variety of other industries. For example, improvements in component material are directly related to the developing technologies of batter-based energy storage. The research and development processes for these new materials can vary widely. The use of heat treatments and furnaces for new materials development requires reliable, safe furnaces.
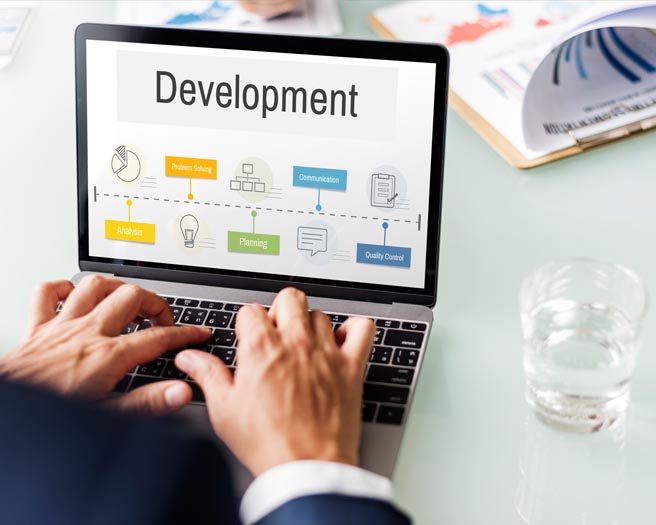
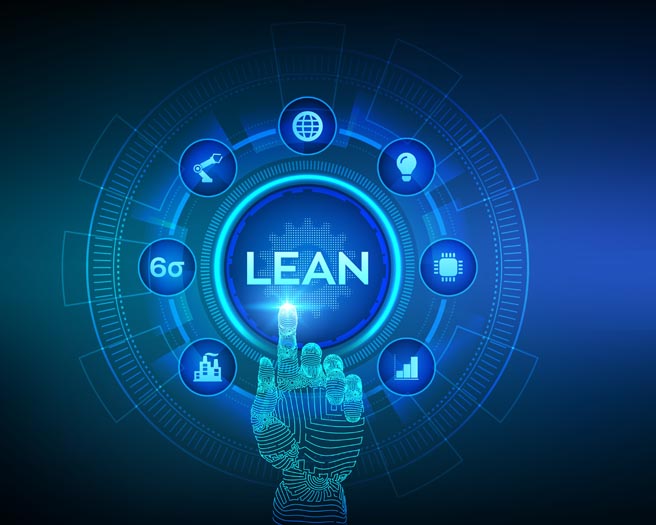
3. Lean concept development
Lean manufacturing is a production method aimed primarily at reducing times within the production system as well as response times from suppliers and to customers. Companies employ the strategy to increase efficiency. Lean manufacturing is a production process based on an ideology of maximising productivity while simultaneously minimising waste within a manufacturing operation. The lean principle sees waste is anything that doesn’t add value that the customers are willing to pay. By receiving goods only as they need them for the production process, it reduces inventory costs and wastage, and increases productivity and profit. The downside is that it requires producers to forecast demand accurately as the benefits can be nullified by min or delays in the supply chain. It may also impact negatively on workers due to added stress and inflexible conditions. A successful operation depends on a company having regular outputs, high-quality processes, and reliable suppliers. Waste in industry, whether that is idle workers, poor processes or unused materials is a drain on productivity, and lean manufacturing aims to eliminate this. The motives behind this vary depending on opinion, from increasing profits to providing benefits to customers.
4. Product, Production and process optimization in Manufacturing
Product optimization is the process of refining and improving a product to make it more valuable to current users and more attractive to new ones aiming to optimize your product pre-launch during the initial development. The process should continue after the product hits the market and until your company sunsets it. Product optimization is never complete, and you should weave it throughout your product’s lifecycle.
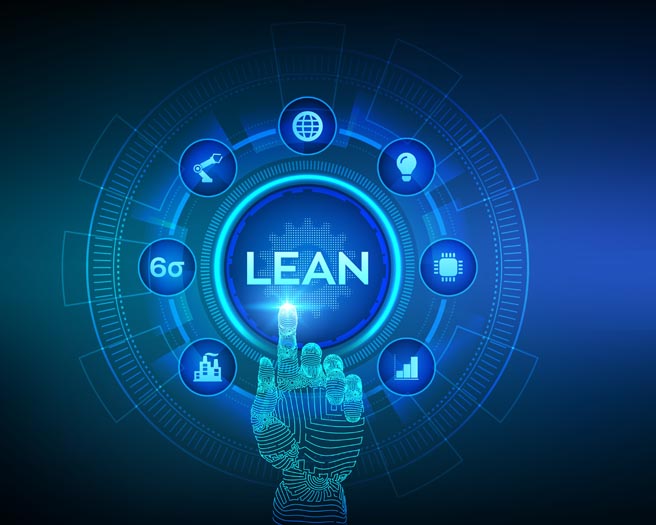
Production optimization is a collection of activities designed to increase productivity in the production system. It’s separate from process optimization, where the optimization effort is focused on making the finished product more efficient in its stages. Production optimization uses models, analysis, prioritization, and measurements to increase productivity. This optimization includes equipment, staging areas, inventory protocols, facility layout, conveyance, and more. Optimizing production is a tactic used in large footprint industries such as oil production and gas construction. But optimization can be used in most manufacturing operations for almost any production process to deliver greater value. As IoT technology has matured, companies have discovered that information delivered from real-time data analysis allows them to understand the changing conditions and flow of the system and how it can be used to enhance productivity. Companies must use these insights to optimize production rates in the entire production process.
The most significant difference between process and production optimization is that process optimization eliminates unnecessary steps in a specific process step within the production system. It’s a product optimization designed to maximize production optimization through increased efficiency for that step or sub-process. On the other hand, production optimization seeks to optimize the system itself. It may use models based on real-time data to look at flow rates, machine layout, labour utilization, and other factors to improve the physical performance and layout of the entire production system.
Process optimization will include steps such as:
- Identifying problems specific to the process
- Analyzing the current state to create the desired state
- Auditing the change to see results
- Monitoring the change to keep it on track
Production optimization will include steps such as:
- Changing factory layout
- Changing or rearranging machines and tools at point of use
- Implementing new WIP procedures to reduce inventory
- Training operators and technicians towards automated alarms and monitoring system to eliminate old habits
- Developing new internal inventory delivery procedures
5. Digital Manufacturing
Digital manufacturing is an integrated approach to manufacturing that is centred around a computer system. The transition to digital manufacturing has become more popular with the rise in the quantity and quality of computer systems in manufacturing plants. As more automated tools have become used in manufacturing plants it has become necessary to model, simulate, and analyze all of the machines, tooling, and input materials in order to optimize the manufacturing process. Overall, digital manufacturing can be seen as sharing the same goals as computer-integrated manufacturing (CIM), flexible manufacturing, lean manufacturing, and design for manufacturability (DFM). The main difference is that digital manufacturing was evolved for use in the computerized world.
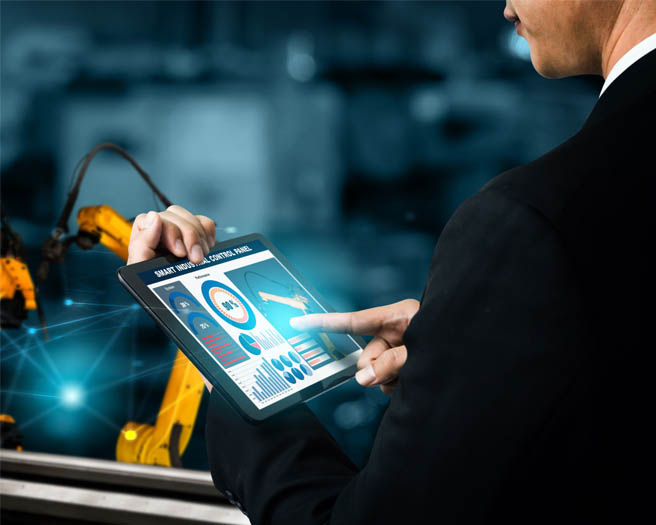
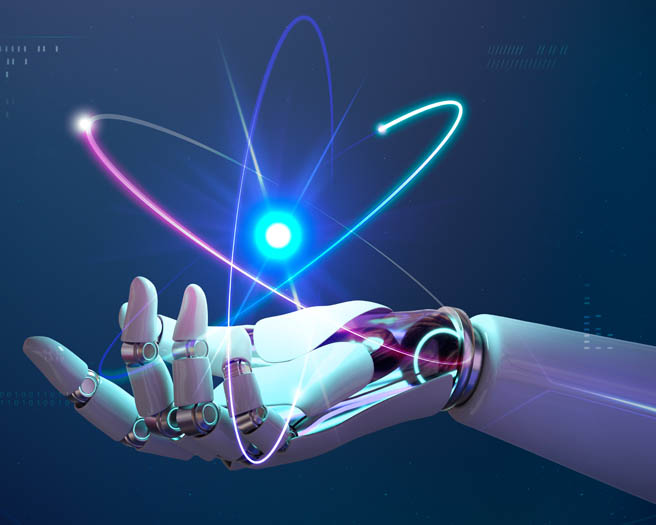
6. Robotics
Robotics is an interdisciplinary branch of computer science and engineering. Robotics involves the design, construction, operation, and use of robots. The goal of robotics is to design machines that can help and assist humans. Robotics integrates fields of mechanical engineering, electrical engineering, information engineering, mechatronics, electronics, bioengineering, computer engineering, control engineering, software engineering, mathematics, etc.
7. Artificial Intelligence
Artificial intelligence (AI) refers to the simulation of human intelligence in machines that are programmed to think like humans and mimic their actions. The term may also be applied to any machine that exhibits traits associated with a human mind such as learning and problem-solving. The ideal characteristic of artificial intelligence is its ability to rationalize and take actions that have the best chance of achieving a specific goal. A subset of artificial intelligence is machine learning, which refers to the concept that computer programs can automatically learn from and adapt to new data without being assisted by humans.
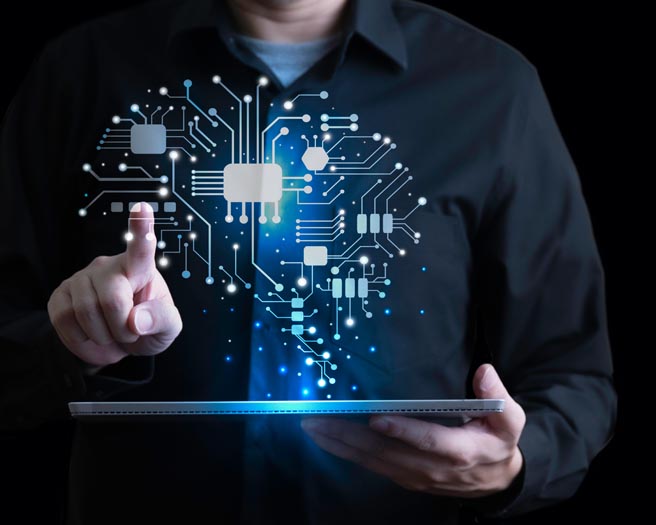
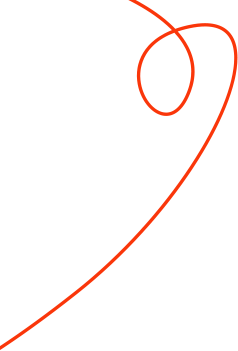
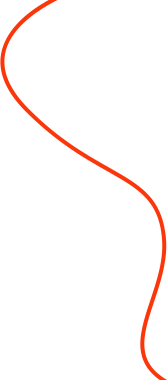